The Lifeline of Productivity: Why Aftermarket Support is Non-Negotiable for Pallet Wrapper Machines
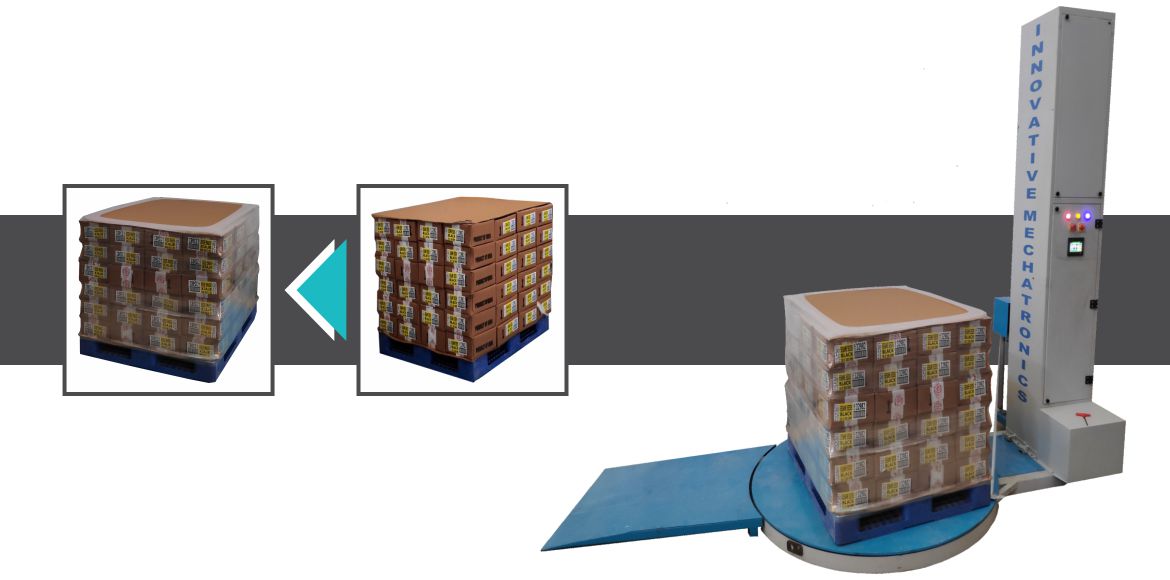
A pallet wrapper machine is more than just a piece of equipment; it’s a crucial component in the smooth operation of many businesses. Investing in one is a significant step, but the real key to maximizing its value lies in the aftermarket support that accompanies it. Aftermarket support is the ongoing care and attention provided by the manufacturer or supplier after the initial sale. It’s the safety net that ensures your machine continues to perform efficiently and reliably for years to come. Without it, you risk costly downtime, premature machine failure, and a diminished return on your investment. This blog post will explore why aftermarket support is absolutely essential for any business utilizing pallet wrapper machines.
A cornerstone of any effective aftermarket program is proactive and preventative maintenance. Regular maintenance isn’t just about fixing issues as they arise, it’s about preventing them from happening in the first place. This includes tasks like regular lubrication, cleaning, inspection of key components, and timely replacement of worn parts. A robust aftermarket support program will include customized maintenance plans tailored to your specific machine model and operational environment. These plans often involve scheduled visits from qualified technicians who can assess the condition of your machine, identify potential problems early on, and ensure that all systems are functioning optimally. Proactive maintenance greatly increases the lifespan of your machine and significantly reduces the risk of unexpected breakdowns that can cripple productivity and lead to costly repairs. Having proper maintenance also means that you can leverage the knowledge of the technicians, as they may be able to identify small tweaks and adjustments to make your machine more efficient. When selecting a provider, the availability and ease of access to replacement parts is a crucial consideration. Genuine, manufacturer-approved parts are essential for maintaining the integrity of your machine, while using inferior parts can compromise its performance, lifespan and safety. A commitment to parts availability and proper documentation on behalf of the Pallet Wrapper Machine Manufacture is crucial for the overall health of the equipment.
Access to reliable technical assistance is another crucial aspect of comprehensive aftermarket support. No matter how well-maintained a machine is, there may be instances where unforeseen issues crop up. The ability to quickly connect with a skilled technician who can diagnose and resolve problems remotely or on-site is absolutely essential. A solid program will provide various channels of contact, including telephone, email, and online portals, so you can get prompt support whenever you need it. Remote support, utilizing diagnostic software and real-time video conferencing, is becoming increasingly popular. With this method, technicians can assess the machine’s condition, provide troubleshooting guidance, and in many cases, resolve the issue without requiring a physical visit. Comprehensive documentation, including machine manuals, schematics, and troubleshooting guides, also empowers your in-house team to address minor problems quickly. Proper training for operators and maintenance personnel is also an important part of a complete program. Well-trained staff can operate and maintain machines properly, reducing the risk of user errors and contributing to the long-term reliability of your equipment. If your business deals with other types of wrapping solutions such as wires and cables, then it is beneficial to understand the support options for all the equipment, such as a Cable Wrapping Machine to help streamline the overall workflow.
Beyond the basic support and maintenance, a comprehensive aftermarket program will also include continuous upgrades and enhancements to keep your pallet wrapper machine up-to-date with the latest technology and performance standards. This can involve software upgrades that improve the machine’s operational capabilities, hardware improvements that enhance its reliability, or adjustments to machine parameters that can increase its output. This kind of forward-thinking approach helps your machine remain efficient and prevents obsolescence. As your business grows, you may need to adapt your machine to meet new requirements, and this may include making adjustments to the wrapping pattern, tension settings, or the type of film you’re using. A comprehensive support team will assist you in making these changes, ensuring your machine can adapt to your needs. It’s also important to consider the overall packaging needs of your facility. Understanding the support needed for machinery like a Plastic Wrapping Machine can also ensure your entire wrapping process is running efficiently.
In conclusion, aftermarket support is not an optional extra, it’s a critical investment that ensures continuous and reliable performance of your pallet wrapper machine. It’s about safeguarding your initial purchase, minimizing costly downtime, and maximizing the productivity and efficiency of your packaging operations for years to come. Choosing a supplier that offers a comprehensive aftermarket program should be a crucial consideration. With the correct support in place, you can be confident that your pallet wrapper machine will continue to serve your business effectively. For comprehensive pallet wrapping solutions and unmatched aftermarket support, contact Innovative WrapTech Pvt. Ltd. today.